Our Business Activity
Van Hessen is the leading global player in the harvesting, processing and distribution of natural casings, meat products and raw materials for the pharmaceutical industry. Thanks to the worldwide operation of gutrooms inside slaughterhouses, we are able to operate closely to the source and secure a constant flow of raw materials for our customers. Controlling and supervising all steps in the supply chain enables us to ensure the quality of our products and services.
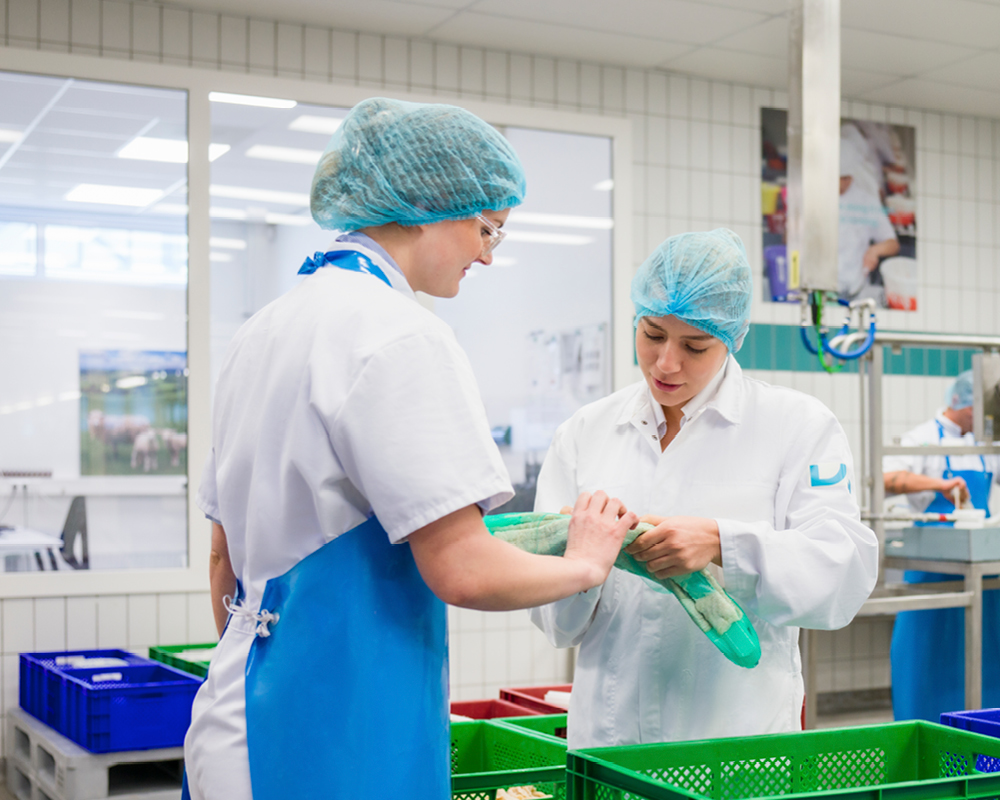
Our Sustainability Strategy
At Van Hessen, we take an all-encompassing approach to sustainability, comprised of environmental, labor, ethical and procurement related topics. While we pursue a holistic understanding of sustainability, we systematically identify focus areas and define strategic priorities in order to guide our decisions and actions. Our materiality analysis is the key instrument in this regard.
The year 2022 was a massive leap forward for the sustainability initiative at Van Hessen. Building on the foundation of our materiality assessment, our Global Management Team formed our sustainability strategy to ensure that our key focus areas are given the support needed to bring our vision to reality.
One of the key priorities of the sustainability team during 2022 was the awareness and communication of our sustainability objectives and the visibility of the principles of sustainable development in our corporate strategy.
We recognize that the cornerstone of sustainable progress is a fundamental understanding of current performance. Our Van Hessen team took measures to lay the groundwork for a systematic non-financial reporting system by also collaborating with the Group level to measure our consumption for scope 1 & 2 facilities. This planned reporting system will be rolled out to full effect in order to establish a complete baseline that we can use to quantify all of the progress made from our future project and developments.
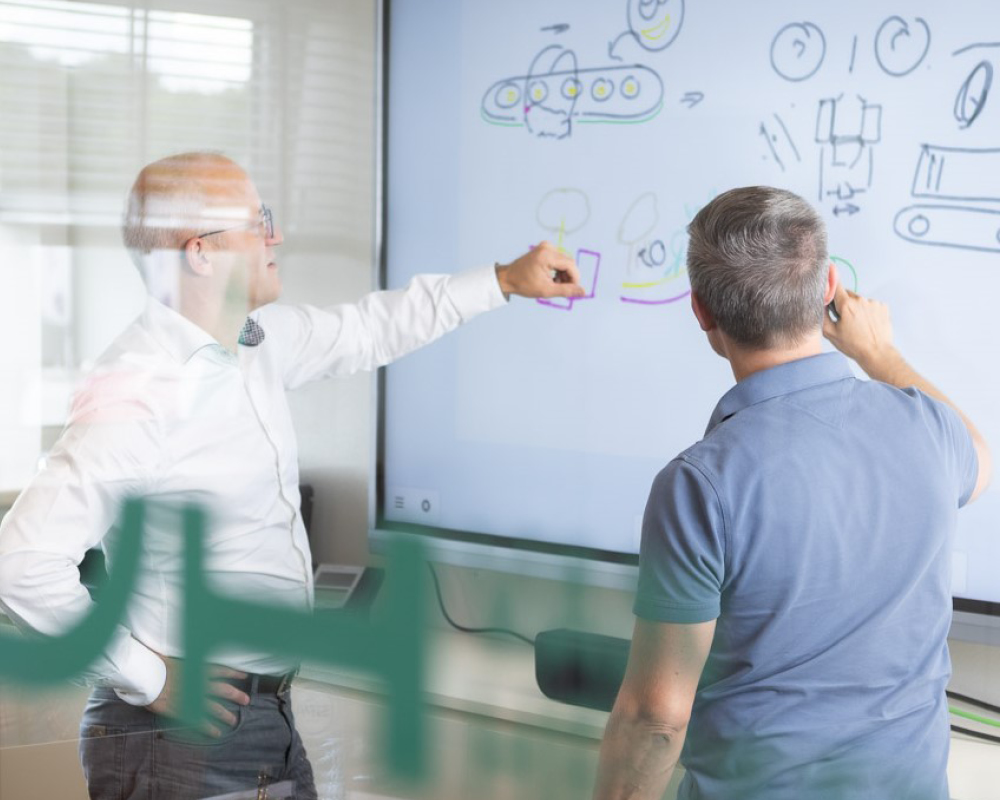
Van Hessen is known for upholding some of the highest standards in food safety. Certifications vary by region and individual location, but we have a plethora including: BLK, BRC, HACCP, IFS, MCS, SAE, FSC 22000.
Van Hessen Sustainability Organization
Materiality Assessment
In 2021 and 2022, we conducted an internal materiality assessment jointly with a consulting firm and determined key focus areas for our sustainability strategy and operations. This assessment began with insight from industry materiality maps provided by the Sustainability Accounting Standards Board (SASB) and MSCI to obtain a profound understanding of potential material topics. In our second step, we held a series of interviews and workshops with managers from different areas to analyze the importance of individual topics according to two dimensions:
-
What economic, social and environmental impact do we make through each material topic? The larger the impact, be it positive or negative, the more salient the topic.
-
What is the relevance of each topic for Van Hessen from a business point of view? Here we analyzed the extent to which the topic potentially contributes to our success.
Overall, we identified and allocated twelve material topics in our materiality matrix. In a subsequent step, we analyzed the topics further and defined a materiality threshold for identifying the sustainability topics of strategic relevance.
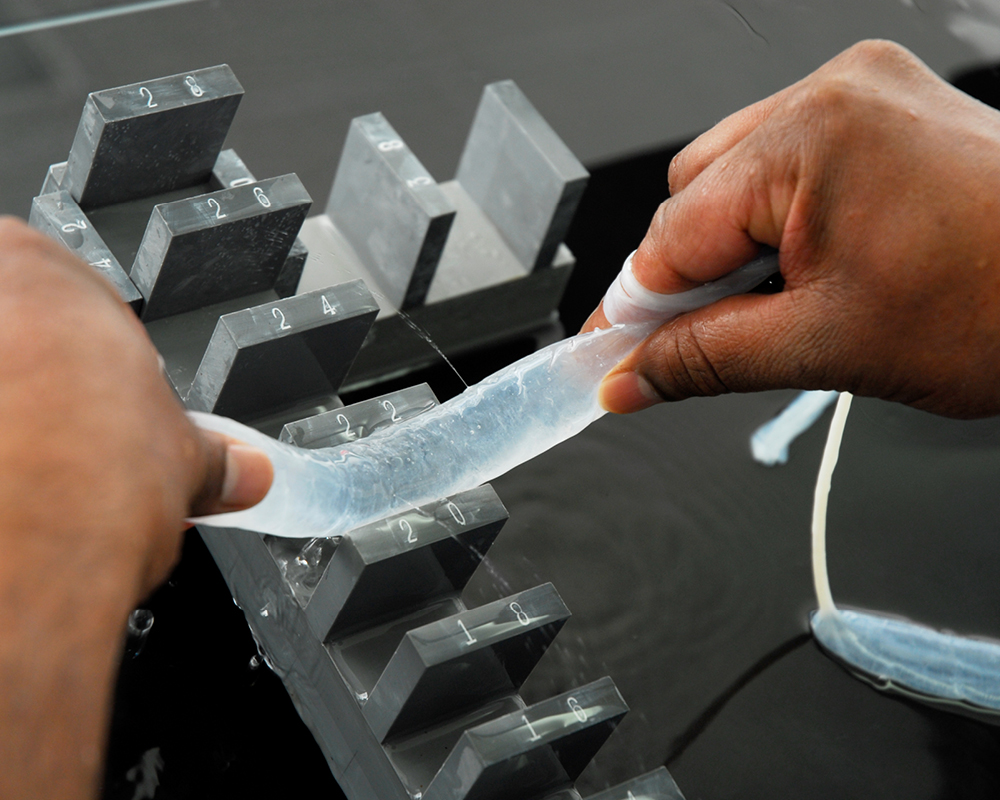
Materiality Matrix
Our Material Topics –
Activities and Accomplishments
Regarding environmental topics, Plastic Waste & Recycling Opportunities are of prime importance to us considering our business model, which is based on using materials that would otherwise go to waste and turning them into valuable products. At the same time, we try to reduce our use of plastic. To that aim, our Selection and Gutroom Competence Centers are constantly pushing innovation. A recent process optimization regarding the use of plastic rings for our net products is expected to save 4.8 million of these rings every year. That corresponds to a remarkable 12,000 kg of CO2 equivalents (CO2 eq) eliminated from our total carbon footprint.
Reducing our Greenhouse Gas Emissions (GHG) is one of our most important goals, considering the challenges brought about by global warming. This is why we are keen to use the opportunities provided by our facilities for generating solar energy. One of the largest projects we finalized in 2022 was the installation of solar panels at our headquarters in Nieuwerkerk aan den Ijssel. We equipped our roofs with a total of 1,262 panels which will enable us to produce almost 500,000 kWh in the first year of operation.
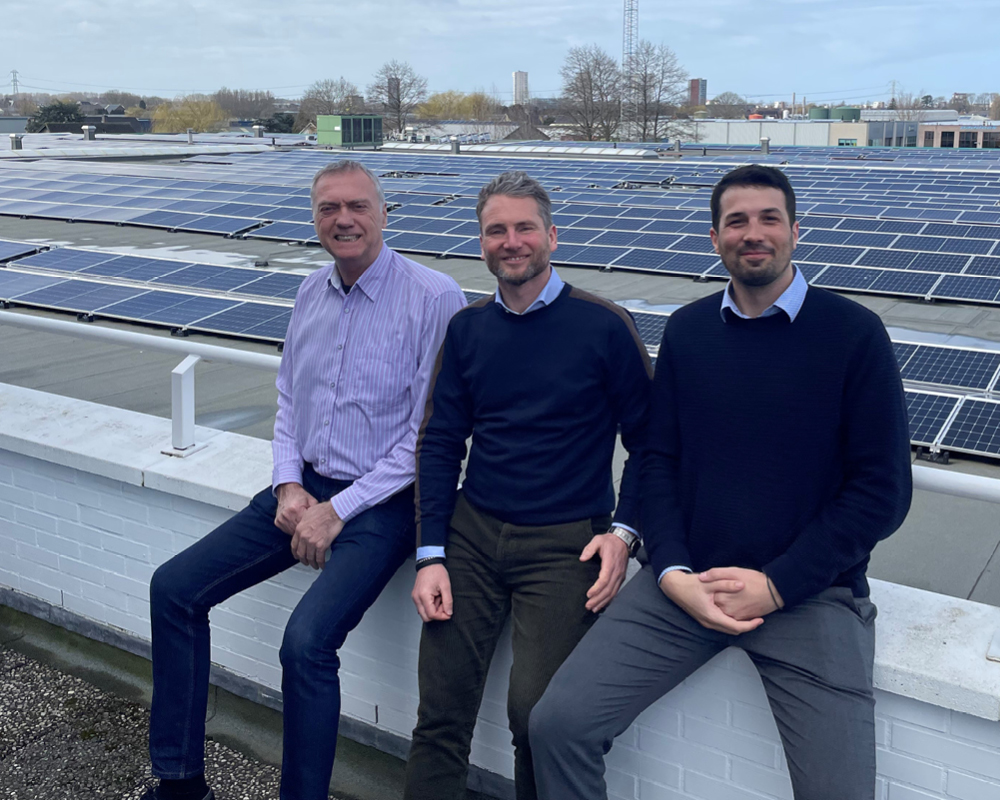
Our recent installation at the Van Hessen HQ has transformed our energy usage while also providing the local grid & community with excess renewable energy.
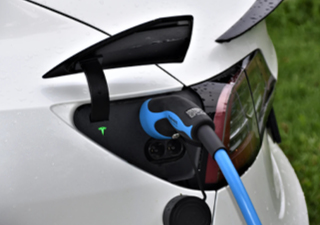
We have a new policy that all company lease cars must now be electric vehicles, with the added benefit of using charging stations at our headquarters that make use of solar power from our recent installation.
Such projects are also a vital part of our Energy Management, since they allow us to secure the energy supply of our operations. As 2022 has shown us in particular, the supply of fossil fuels is far from secure, not to mention the substantial price fluctuation we witnessed on European energy markets. We are proud that the project will not only accelerate Van Hessen’s renewable energy transition, but will also contribute to our local Zuid-Holland community’s access to renewable energy with an estimated annual 315,800 kWh that will be put back on the grid.
At Van Hessen, we seek to reduce our environmental footprint by reducing emissions, and we are meticulous in our efficient use of resources. In terms of our Water & Chemical Management, we seek to implement environmental management systems at our locations to systematically assess and improve our environmental performance. Doing so is nothing new to us. Our supply point in Toledo, which is one of our largest facilities, has been ISO 14001 certified since 2005, and we are planning to have the management systems at other locations certified according to ISO standards as well.
Where labor-related issues are concerned, Employee Health & Safety is of utmost importance to us. At all of our locations, we ensure that our employees work in a safe and healthy environment. We maintain the highest safety standards by always pursuing innovations. A prime example of this is the collaboration between our global health and safety department with our machinery manufacturer to increase the safety of the equipment our people are working with. The project team also assessed our use of chemicals and related processes in order to improve the respective protection equipment.
However, we do not rely solely on assessments conducted by specialists and external parties. We also directly engage with our people to ask them for their perception of the Working Conditions we provide. In 2022, we launched a comprehensive survey among our employees in the Netherlands, which we will be repeating on a biannual basis and extending its scope to other locations. We achieved a response rate of 74%, outperforming industry benchmarks. The high response rate reflects the engagement of our people and their willingness to provide feedback. The results will help us to initiative improvements on two levels. We will work with regional management teams to address key focus areas informed from the region-specific survey responses. On a global level, we have a global development team that will analyze key focus areas and determine steps to improve group-wide.
At Van Hessen, it is not only important for us to ensure the safety, health and well-being of our people, we also try to provide them with opportunities to develop personally and professionally. Career Management & Development is another material topic for us. In particular, we make every effort to promote the development of our employees, which is represented in our long-standing traineeship program, preparing our new team members for careers in different areas:
-
Management Traineeship: the goal of our Management Traineeship is to prepare the participants for a key position within the Van Hessen Group. They travel around the world for about 18 months, learn everything about the production lines and production processes, and become acquainted with the different management areas.
-
Trainee Product Specialist (Sourcing): our Product Specialist (Sourcing) Trainees learn everything about our product and manufacturing operations. This way they become valuable advisors in the field of product specifications, processes and procedures.
-
Trainee Product Specialist (Selection): trainees in the Product Specialist (Selection) Program get to know global production environments to manage the optimal products and best processes. Becoming experts in innovative product solutions and process improvements, they are the ones preparing our business for expected and unexpected changes in the market.
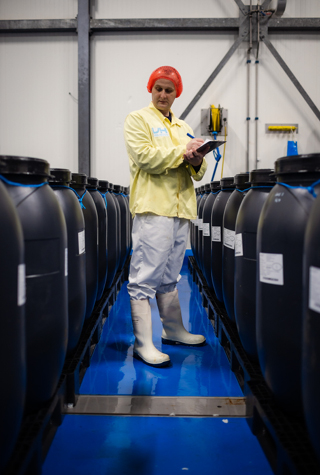
Assessing risks and ensuring safety. Our Health and Safety team's meticulous approach to risk assessment and procedural improvement ensures that we are doing everything we can to maximize the safety of the Van Hessen work environment.
Spotlight on Career Management and Development
Looking Ahead
One major aim for the upcoming years is to keep on growing the active involvement of our internal and external stakeholders. We will expand the scope of our employee survey and also encourage more employees to use the internal communication channels that we have established to provide our people with a platform they can use to raise a sustainability issue or concern and make suggestions on how we can further improve our sustainability performance.
We will begin to engage external stakeholders this year and beyond to collaborate on innovation that will advance sustainable progress within our industries. We are also planning to improve our sustainability communication by introducing a newsletter to keep stakeholders updated on our progress and help building a dialogue across our industry.
The reduction of GHG emissions will represent a crucial focus area. We will continue working on gaining a better understanding of our Scope 3 emissions as a basis for systematic measurement and improvement. Thus, we will begin to engage with individual suppliers who have a significant ability to help us move the needle.
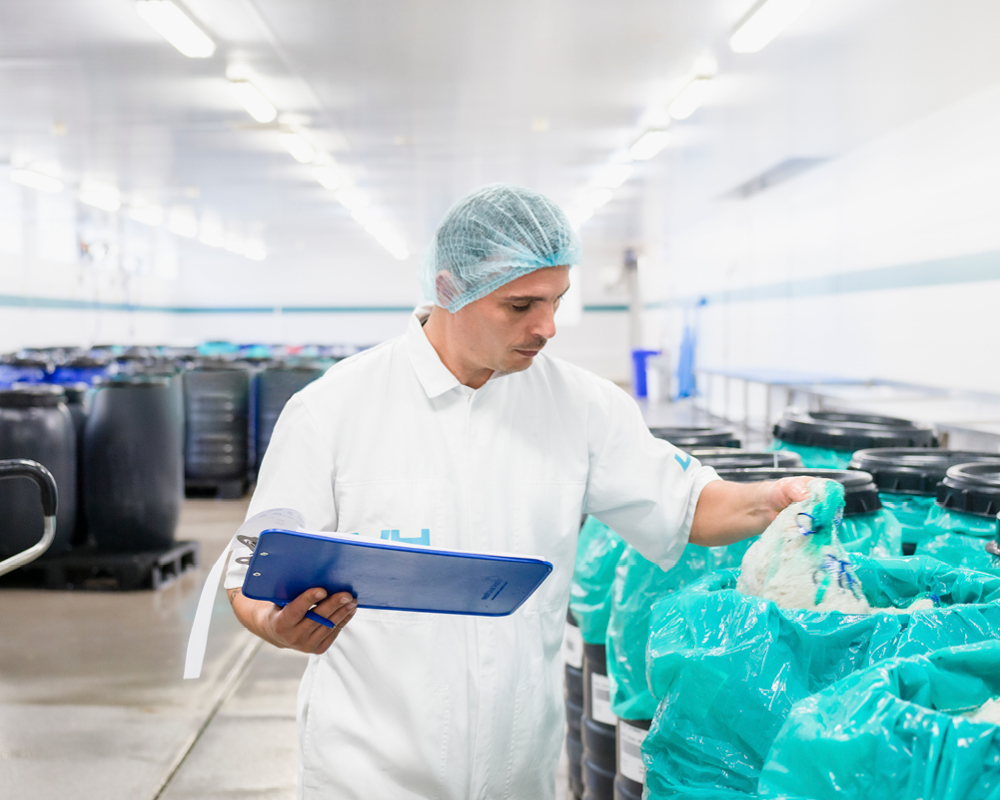
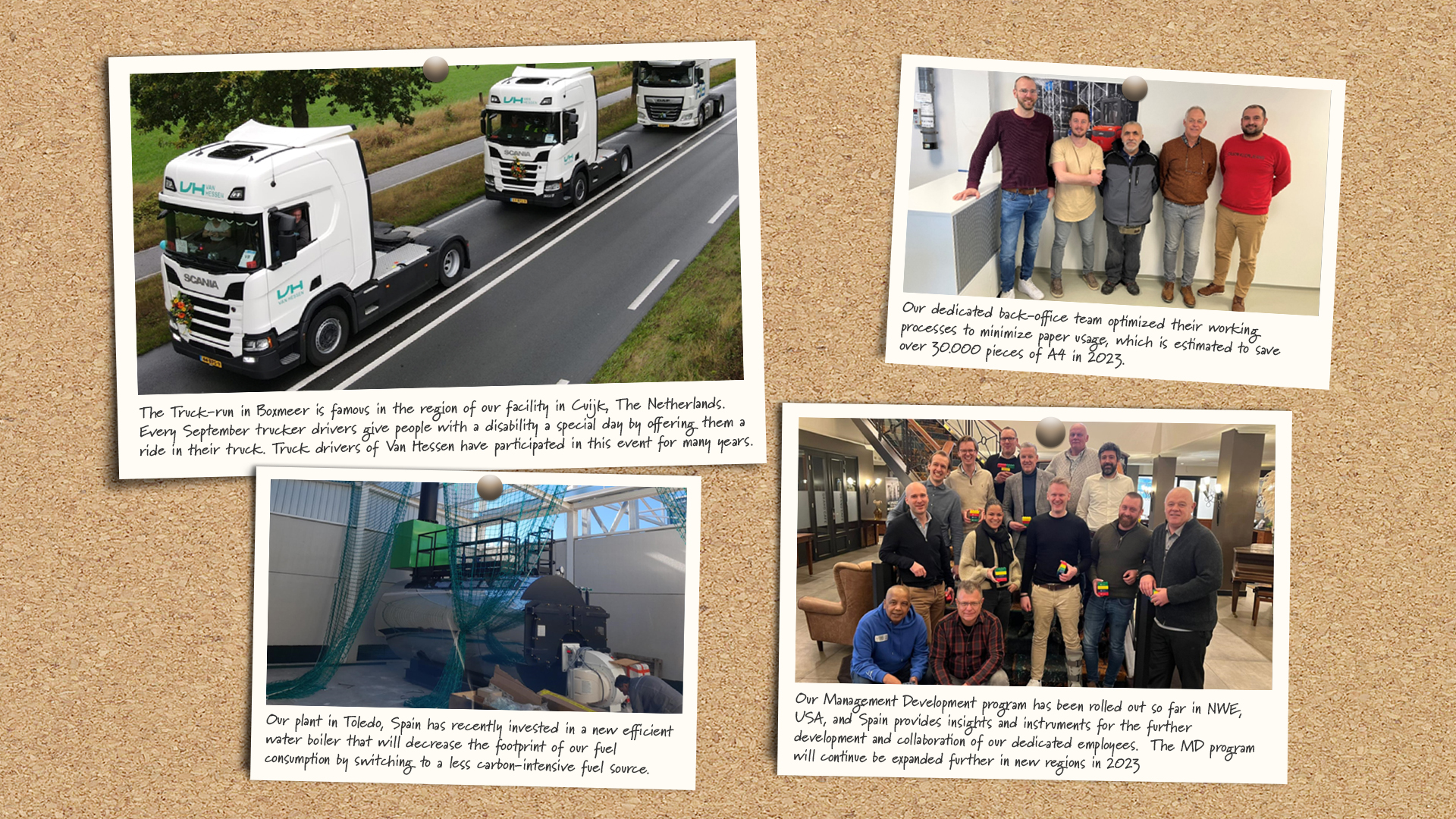